2500BPH Complete Bottle Water Production Line
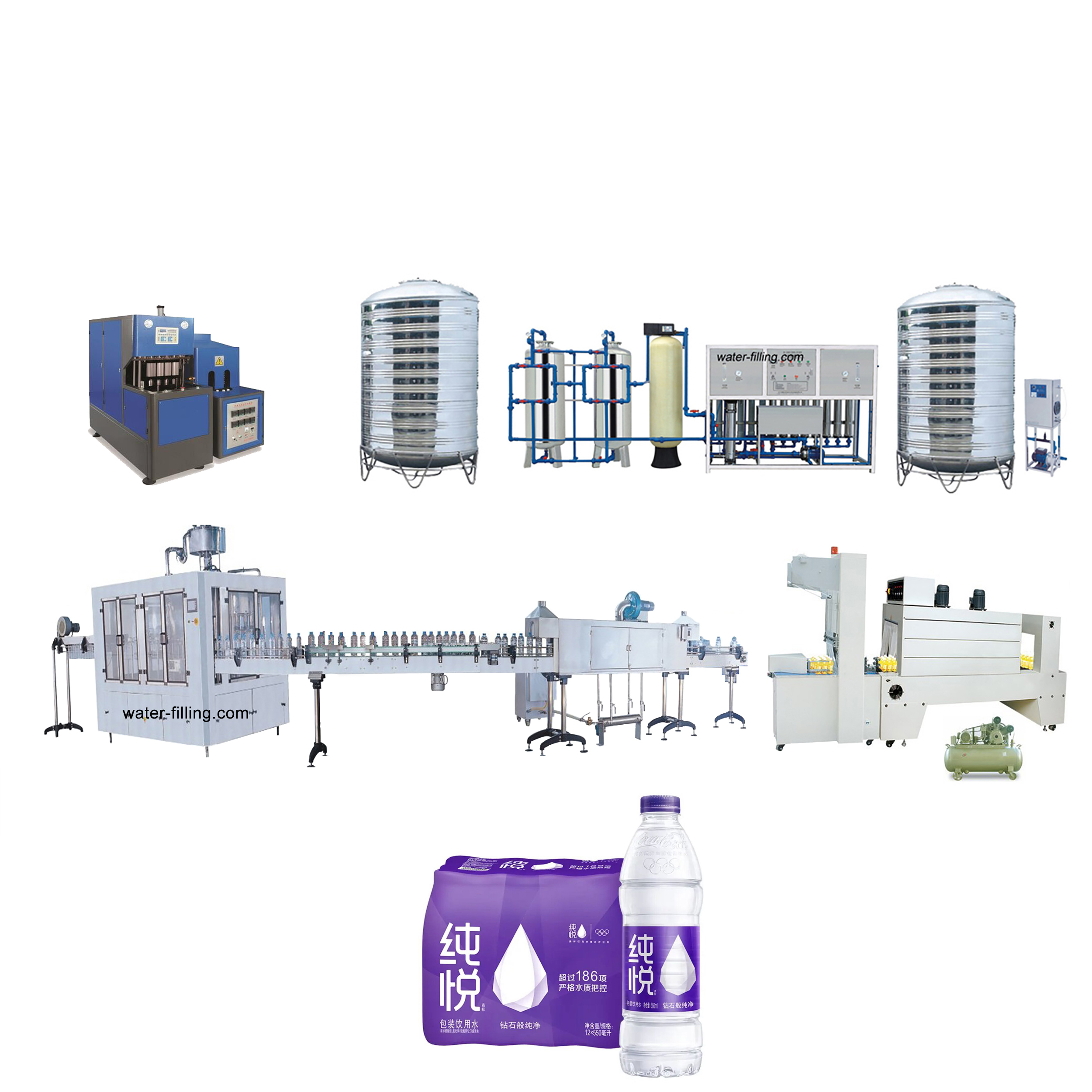
Setup an bottled water production line with less cost but more big capacity. NEP-S2500 water bottling plant cost just half of an fully automatic 2000BPH bottled water production line. Only take a few more labor. But its capacity is double than the 1000BPH bottled water production line.
2500 bottles per hour * 24hour=60000 bottles per day
Both blow molding machine and monoblock filling machine are newest type adapt to the needs of the market inquirement. The two machine is the soul bottling machine of the whole water bottling plant.
The blow molding machine capacity can reach 2500 bottles per hour. It is auto fall down plastic bottle so that do not need worker manaul move it. Save large time. It is more convenient.
The monoblock filling machine collect washing filling and capping in one machine. And it is control by PLC. Fully automatic which capacity can reach 2500 bottles.
It is widely use to production purified bottled water, mineral bottled water, vitamin bottled water.
Production capacity | 2500 bottles per hour |
Filling bottle specification: | 200ml-1000ml.(Up1000ml bottle machine need customize,not need premium) |
Container for shipment | 40HQ container |
Labor inquiry | 7 wokers |
Working process of the water production line
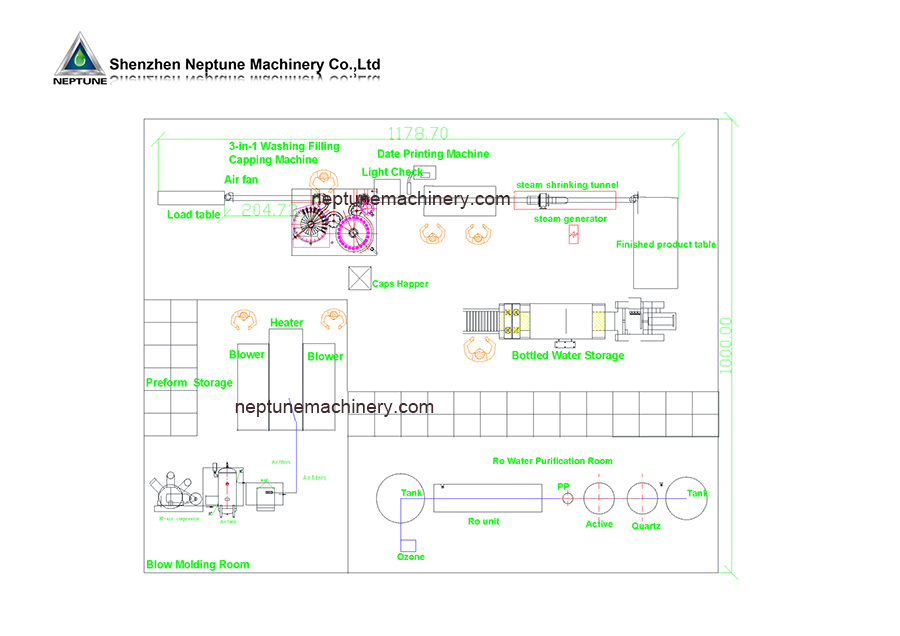
It just need an 12 meter long and 10 meter width production room. You can storage materials and finished production on this production room also. Also can lonely storage finished product divided.
The 120 square meter production room mainly divided to three part. The water purification room, the blow molding room and main filling room.
Ro water purification with ozone and UV system to produce the purified water. Then storage in the pure water tank for filling use.
Woker insert preform on the oven for heating. Then manual move the heating well preform to blowing bottle machine. Then blowing bottle machine will blow wind into preform and making plastic bottle. Bottle will automatic fall down and collect in an box.
Woker need manual insert plastic bottle in the monoblock filling machine. It will automatic sending the bottle to washing by water, filler pure water into the bottle, then capper it. And conveyor to shrinking tunnel. Before bottled water go into shrinking tunnel. Worker need manual sleeve PVC label on every pass bottled water. So that PVC labeling will shrinking and got very tight on the bottled water after go throught shrinking tunnel.
Then worker need collect the bottled water 6/12/20/24 bottles to wrap film and shrinking package by the wrap packing machine.
Every machine of water production line was built for a purpose
Making Plastic Bottle
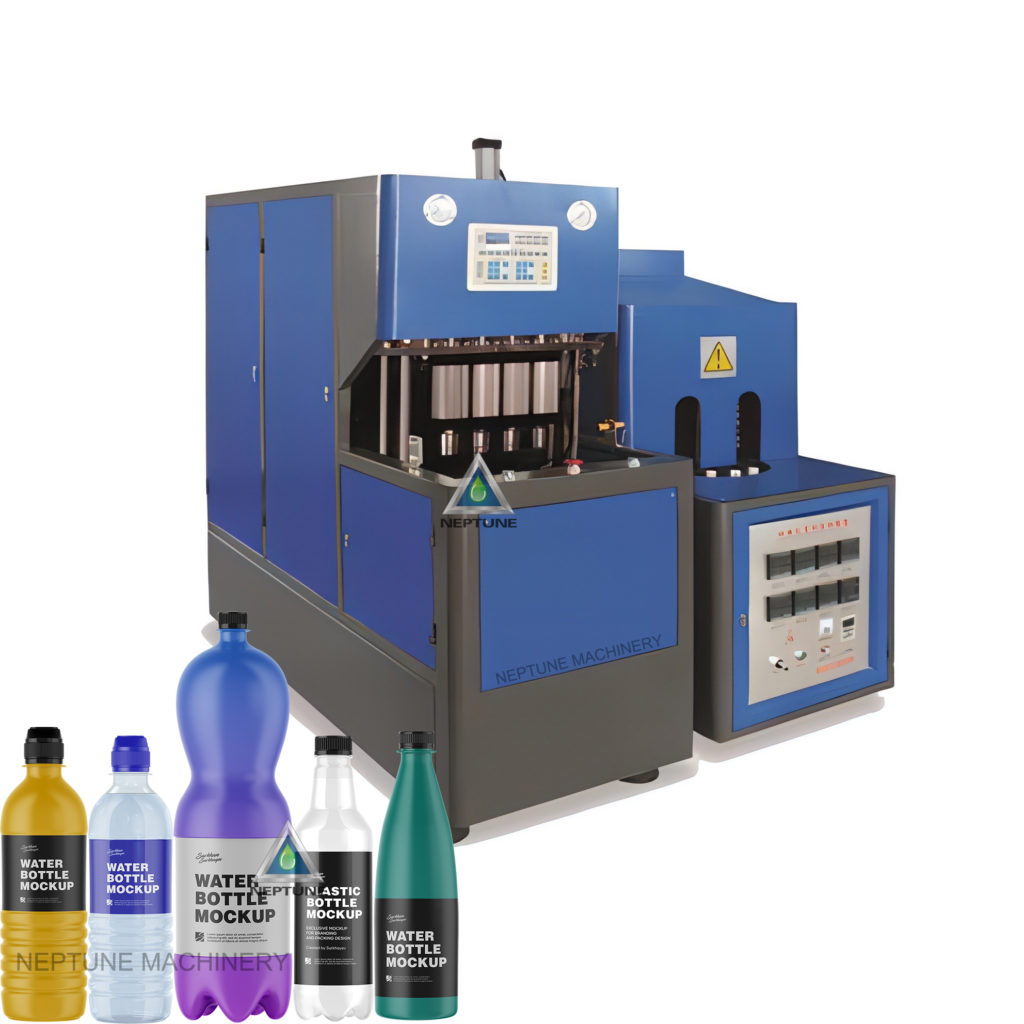
4 Cavity once blow molding machine
It once put and produce 4piece bottle, then auto fall down into idea box with manual hand. Save 1worker, more fast and safe.
It is reliability blowing machine to produce differently shaped pet plastic bottle. An lot mineral water and beverage company use it produce their unique plastic botlle for filler water or beverage. Also, a lot oil company use it production oil pet plastic bottle.
Offer Purifed Water
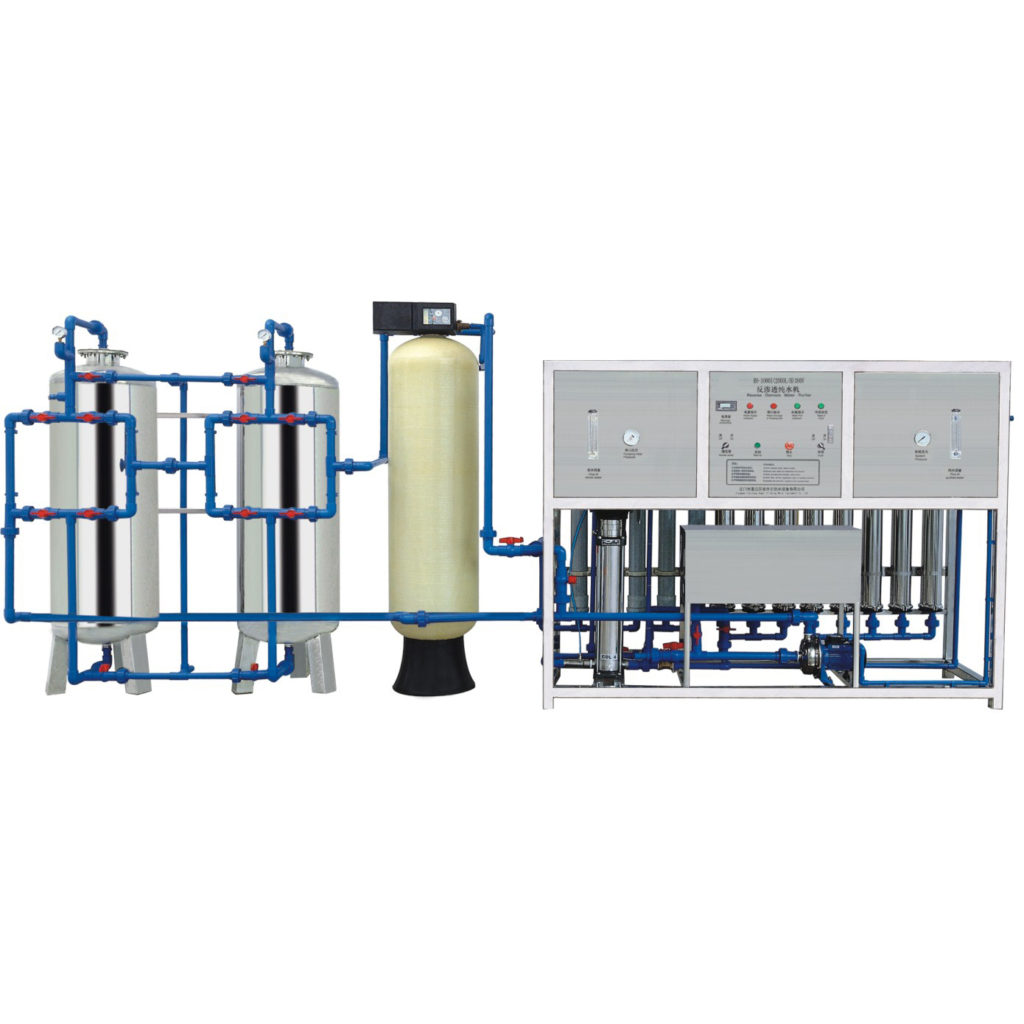
2000 L/H RO water purification machine
It is customized and manufactured according to the local water conditions and flow rate requirements. It utilize an quartz sand filter, active carbon filter, softener, PP filter for the pre-treatment of raw water. The pre-treatment process not only removes order, color and some bacteria, but protects the RO membrane as well, which helps to prolong the life of the RO water treatment equipment and is the main function of the water treatment machine.
Rinser filler capper
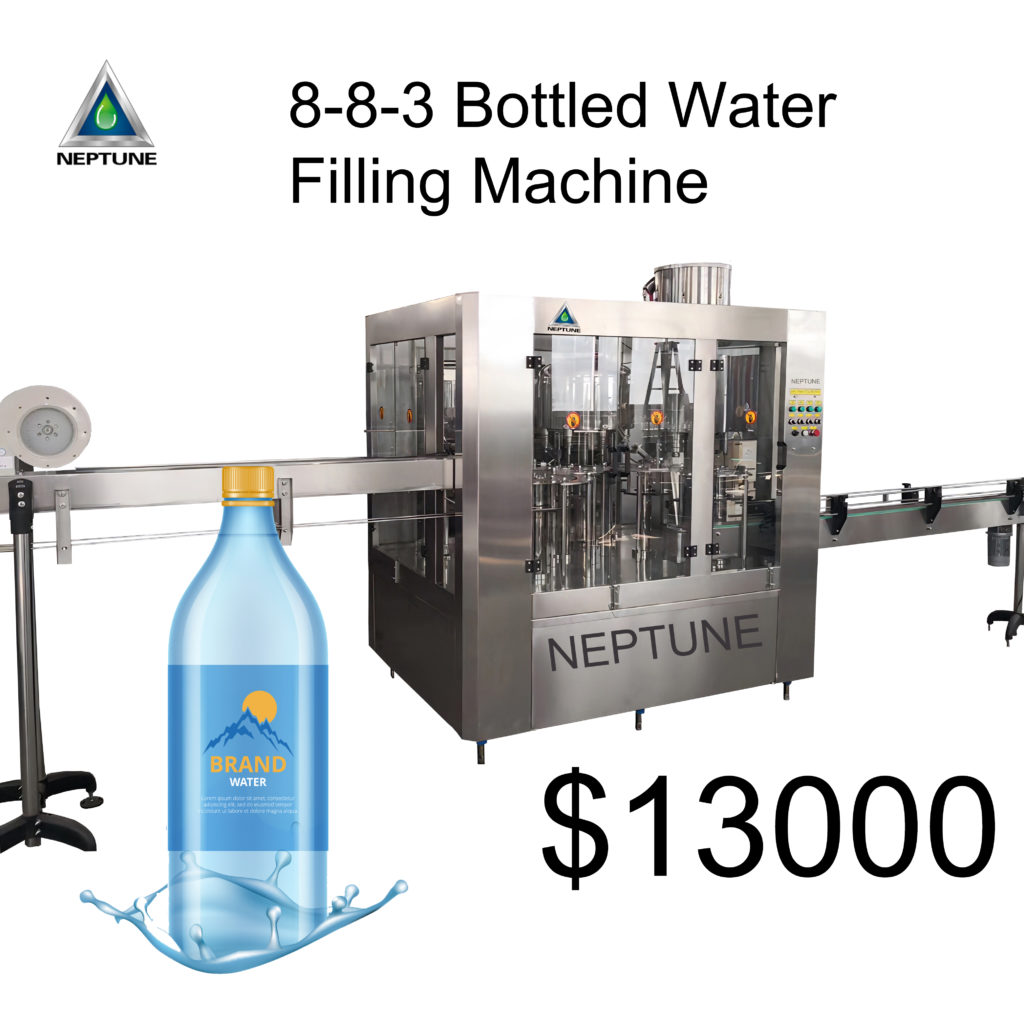
Automatic 8-8-3 washing filling capping machine
It collects washing, filling and capping together. It is an ideal no-gas liquid filling production equipment in the country.
It is mainly suitable for filling and capping of round or square polyester bottles.
According to the demands of different specifications of users, it is only changed shape mold and can bottling different plastic bottle water.
Less invest with higher capacity
NEP-2500BPH bottled water production line also come with ink jet printer, semi labeling machine and semi wrap packing machine. Ink jet printer is used for printing produce date on every pass bottled water on the conveyor belt. And semi labeling machine is for PVC sleeve label shrink package. The wrap packing machine is packaged 6-24 bottles in one bag.
Neptune machinery water bottling plant’s capacity is the actual capacity. Every machine capacity bigger than 2500 bottles per hour. And buffer conveyor belt fast without delay. Then final whole plant capacity is 2500 bottles per hour.
Some customer want bigger capacity but less cost. Also want save 2-3 labor compare with NEP-1000BPH water bottling plant. So the nep-2500bph prefect fit these demand. It is just expensive 30% of the NEP-1000bph plant with double capacity of production. And it save 2 workers compare with nep-1000bph plant. Its total cost just half of the NEP-2000BPH automatic water bottling plant.
Related Bottling Line
FAQ
Dilivery time
Produce 40days, Every machine is producing at the same time. But the slowest machine will decide whole line producing time. The blow molding machine is the slowest producing machine in NEP-S2500 water bottling line
Capacity of production ?
2500 Bottles per hour depend on 500ml bottled water.
1200bottles per hour depend on 1500ml bottled water
Do neptune company offer oversea installation ?
Yes. We offer engineer aboard installation.
Because recent 3 years covid -19 limit, we only can send Africa branch manager engineer fly to different Country installation. NEPTUNE 100% make sure install well the machine and running well over 10years.
Warranty
Warranty 1year. All-life aftersales.
We still have 15years customer buy spare part from us. NEPTUNE will fast DHL or Fex necessary spare part to any Country.
What production room needed for 2500bph water production line?
It just need an 12 meter long and 10 meter width production room. You can storage materials and finished production on this production room also. Also can lonely storage finished product divided.
The 120 square meter production room mainly divided to three part. The water purification room, the blow molding room and main filling room.